Paul Badeau, Applied Fiber, USA, explains why fibre pendants are being adopted by dragline and shovel operators.
The adoption of new technologies is often a long and sometimes difficult road, but fibre pendants are now being seen as a proven technology with a long list of demonstrated benefits.
Synthetic fibre main support pendants
Synthetic fibre main support pendants were first considered for development over 12 years ago. At the time, it was recognised that a reduction in weight aloft could greatly improve dragline performance as it would allow for increased capacity or reduce the working load of the machine. As mine operators are always looking for improvements, these two benefits alone were a strong catalyst to move forward and build the first synthetic main pendants for a dragline.
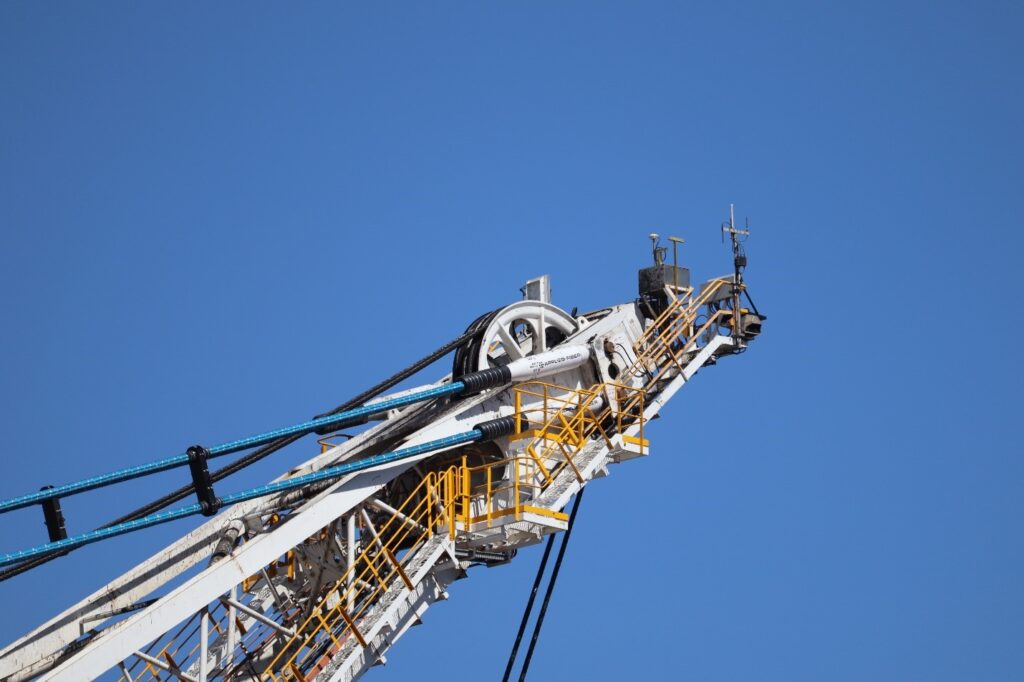
Case study: Antelope Mine, USA
The product was first adopted by Cloud Peak Energy, now NTEC. Applied Fiber designed, built, and successfully installed the first set of mains at the Antelope mine in Wyoming over five years ago.
While the pendants were originally developed to take advantage of the weight reduction fibre would provide by increasing production capacity, numerous benefits have been noted beyond the production gains.
Fibre is multiple times lighter than steel and has reduced sag weight, and this combined with fibre’s natural damping properties has proven to be a huge benefit as the pendants no longer bounce or ‘jump rope’ like steel does. Formerly, the constant jumping of a large mass of steel also caused the lattice boom to also bounce around, creating all kinds of stresses in the dragline boom structure and throughout the machine. Cyclic fatigue is one of the key contributors to metal cracking and fatigue of the structural components.
The first set of fibre mains were installed and a change was immediately noted. The bounce and jump rope effect were nearly eliminated with the fibre pendants, and the boom movements were quietened dramatically. This has had a substantial reduction of fatigue and stress on the structural components. The difference between steel and fibre can not only be seen at a distance, but felt by operators – many of whom have reported significantly reduced movement and vibration in their cab.
Over time, it became evident that the machine was seeing less vibration and cyclic fatigue damage. Draglines converted to fibre were no longer seeing any fatigue cracks or cracking in the boom. A scheduled maintenance outage to weld the boom lacing was eliminated as the fatigue had been so greatly reduced. In time, it was also noted that maintenance crews were not going out and performing welding on the catwalks, railings and steps on the machine, a constant and accepted maintenance issue at most mines.
NTEC calculated a conservative week’s worth of added dragline productivity per year, as it was now possible to skip the outage planned for lacing welding – previously a normal occurrence and scheduled part of the maintenance plan. Furthermore, the company has had no major welding repairs in the lacing since installation. This benefit alone was enough to make the change, and no one had even considered this benefit when they were first installed.
In light of the success of this initial trial, all NTEC draglines ready for changeout have since been converted to fibre.
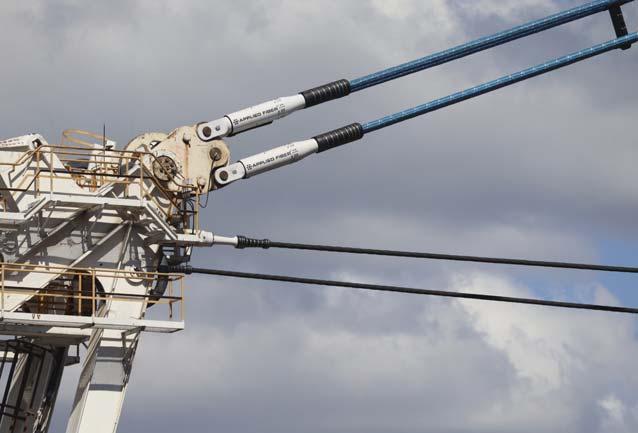
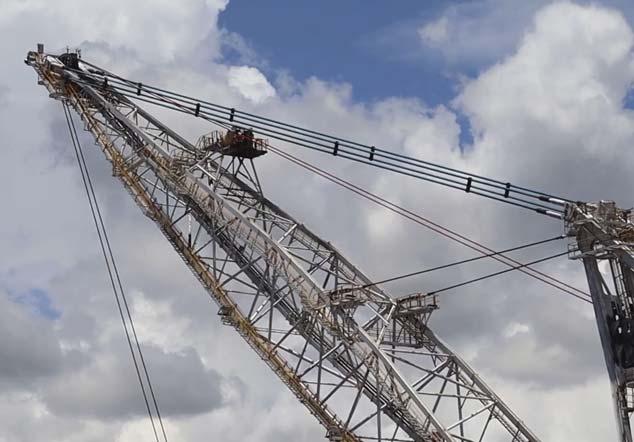
Industry leadership adoption: The new standard
Following years of evaluation, a company with the largest dragline fleet in the world is making fibre main pendants the go-forward standard product for its fleet. The company has installed Applied Fiber main and IBS pendants (Figure 2) on both Marion and Bucyrus draglines, and are already seeing first-hand the benefits for production and maintenance, with the dragline ‘quietened’ down significantly (Figure 3).
Numerous mining machine operating companies are now looking to adopt this technology for their draglines, as the evidence continues to grow in support of large financial gains with fibre pendants.
Fibre main and IBS pendants are now also standardly available through industry wire pendant leader, Bridon Bekaert Ropes Group’s Bridon Tiger Blue fibre product line (Figure 1).
The next realised benefits
More recently through extended data, it has become clear that fibre will not only reduce annual downtime and welding cost, but additionally may have a material impact on the fatigue life of the boom structure and pendant changeout cycle. This means that the boom is not only anticipated to last longer, but if combined with other activities, it is seen as very possible to push out the outage for a boom laydown event. In some cases where other components in the system have been optimised, it is envisioned that a full pendant replacement outage may be skipped.
The ability to materially shift pendant changeouts is based on the added advantage of fibre pendant life. One of Applied Fiber’s goals in developing the fibre pendants with extended life was based around the development of a monitoring system to continuously gauge the life of the pendants. Fibre pendants last longer than their steel counterparts because they have better fatigue properties than steel strand, and, when coupled with a reliable health management
system, pendants can be designed to run longer without introducing new risk. Longer pendant life, coupled with this health management capability, allows a mine to safely push out the planned boom laydown to replace the steel pendants. This is a huge production benefit and creates financial savings for the mine.
While clients first saw the fibre as a means to either increase capacity or reduce welding downtime on an ageing fleet of dragline booms, it has now become clear that there is also the distinct potential to further extend the life of the machines and defer boom laydown events. This opens the door for yet another wave of financial gains for the operating companies. While there are many benefits, some of the company’s clients are realising this may be the greatest financial benefit in adopting fibre.
The maintenance benefits, combined with the production benefits, make it clear that there are many substantial financial gains that come with switching from steel to fibre – despite the difference in cost. Putting a damper in the load path makes the dragline runs better (Figure 4).
The innovation has proven out: dragline operators have increased production capacity; reduced machine stress, fatigue, and structural cracking; reduced maintenance; increased uptime; and extended the life of major components, including the product that was replaced. Additionally, nearly all the dragline operators that have trialed the fibre pendants appreciate and comment on the lack of machine vibration.
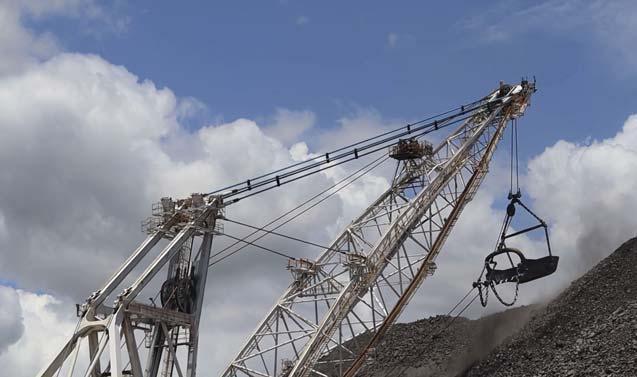
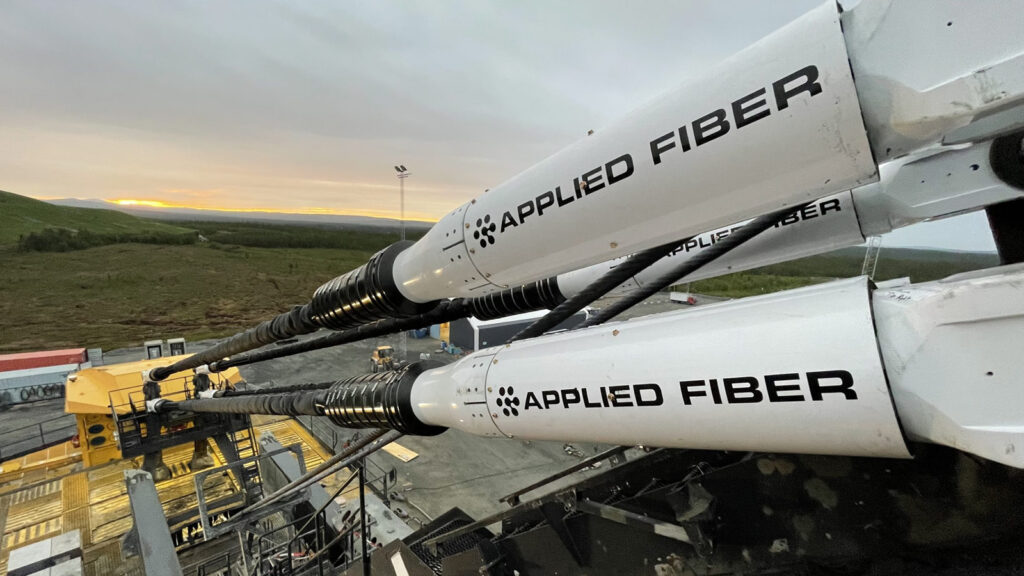
Boom jacking on rope shovels
It soon became clear that the product weight and damping benefits would also translate well for shovels. Applied Fiber recognised that electric rope shovels and their pendants were in many cases replaced more frequently than dragline pendants, primarily because of the frequent shock loading from ‘boom jacking’. Boom jacking is one of the more violent events that a rope shovel can experience in operation. It occurs when the pendants supporting the boom go slack because of the boom being driven upward by the dipper. When the shovel reengages, the boom drops freely, slamming downward and severely shock-loading the pendant cables and the system overall.
While mines always work and train to avoid boom jacking, it is an inevitable part of a rope shovel’s operation, and its effects are quite damaging to the machine over time.
Applied Fiber modified the rope and termination design to create a shock damping pendant set to reduce the impact of boom jacking and vibration for electric rope shovels (Figure 5).
Installed and running for a few years now, the product is proving itself – machines run smoother and the effects of boom jacking are greatly decreased, reducing peak loads from boom jacking up to 52%.
Vibration in the machine is also greatly reduced. Laboratory testing has shown that fibre dampens vibration up to 12 times more than steel. Vibration is a large cause of maintenance issues on shovels. The operators notice the difference too. They can feel the reduction in vibration, which can cause hand and body fatigue over the course of long shifts working the equipment.
Conclusion
Fibre helps machines run smoother and more efficiently, and is well suited for the hard material digging and rough conditions in coal, gold or copper mines, in both hot temperatures in desert environments and frigid conditions of the oil sands and the arctic. Mines worldwide are using pendants and fibre ropes, such as those offered by Applied Fiber, for more and more critical applications. The high strength fibres handle fatigue, reduce vibration and are safer and easier to handle, providing numerous benefits to equipment and their operators.